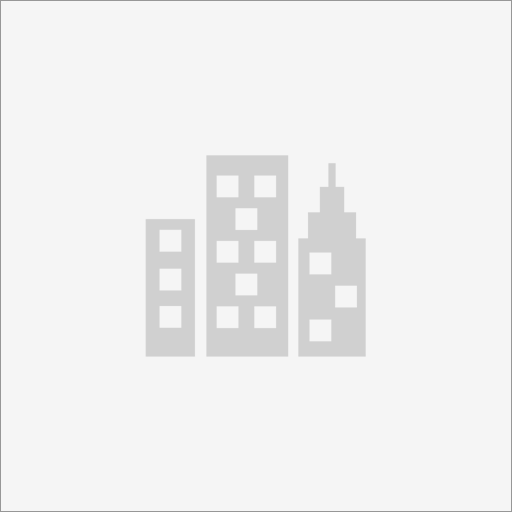
Website Katalyst Healthcares & Life Sciences
Katalyst Healthcares & Life Sciences
Company : Katalyst Healthcares & Life Sciences
Responsibilities:
- Carry out all aspects of a validation project, which includes authoring and executing Validation Master Plan (VMP), Validation Plan (VP), Installation Qualification (IQ), Operational Qualification (OQ), and Performance Qualification (PQ) protocols/report in accordance with established procedures.
- Reviews, approves, and supports validation activities conducted by approved suppliers. Ensures validation records comply with regulatory and corporate requirements.
- Perform Validation Periodic Review for various systems, including automated manufacturing equipment, computerized systems, and test equipment.
- Perform independent evaluation, selection, and application in making adaptations and modifications to projects.
- Receives assigned total project leadership responsibilities on a portion of major significant projects and will be given total management responsibility for smaller projects.
- Manages and provides leadership for the functional group's development, direction, and effectiveness, adhering to organizational policies and processes and supporting overall business and corporate objectives.
- Implements and understands FDA or regulatory requirements as necessary.
- Applies technology principles to multiple tasks. Working knowledge of cross-functional and related technical areas.
- Highlights risk and understand how to approach and complete tasks, avoiding serious delays and considerable expenditure of time and resources.
- Advises team members pro-actively on technical ideas and promotes skill development of teamwork.
- Interacts with peers across projects to secure resources and commitments.
- Handles frequent inter-organizational and outside customer contacts. Represents the organization in providing solutions to difficult technical issues associated with specific projects.
- Follows technical specification requirements and provides feedback on various technical processes and procedures.
- Presents effectively complex technical information/analysis and responds to questions from technical staff members and management.
- Works cooperatively and effectively within a team environment to achieve common goals and results, often influencing the outcome of the team(s).
- Work direction responsibility may include technicians and junior engineers.
- May work with manufacturing and other functional groups on manufacturing and regulatory compliance issues.
Requirements:
- Bachelor's degree or equivalent of education and experience sufficient to successfully perform the essential functions of the job may be considered.
- Bachelor of Science Degree in Engineering, preferred.
- Minimum 4 years' experience.
- Two years of GMP manufacturing experience required.
- Requires demonstrated skills in technical innovation, technical leadership, mechanical and or chemical engineering, fluids engineering, and cellular biology.
- Strong interactive skills in general communication, cross-functional participation, and influence, mentoring and acceptance of guidance, technical leadership, project management, coordination with cross-functional team member, team behaviors, and support for subordinates, junior engineers, technicians, and management.
- Strong technical problem-solving skills.
- Mechanical and electronic ability aptitude to assist with equipment troubleshooting.
- Understanding of and adherence to GMP practices and FDA regulations.
- Knowledge and ability to implement FDA or regulatory requirements as necessary.
- Demonstrated ability to communicate effectively both verbally and in writing.
- Knowledge and use of relevant PC software applications and skills to use them effectively.