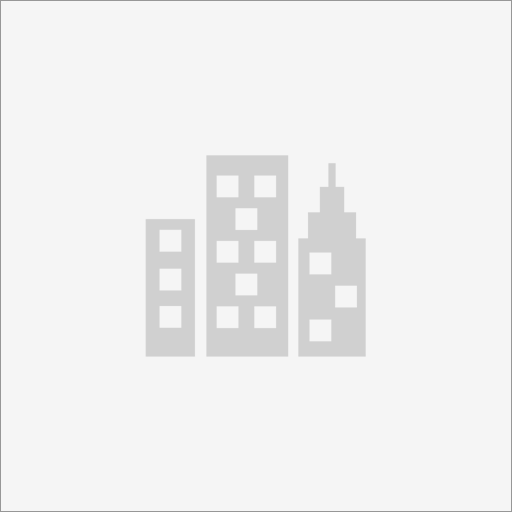
Website Katalyst Healthcares & Life Sciences
Katalyst Healthcares & Life Sciences
Company : Katalyst Healthcares & Life Sciences
Responsibilities:
- Develops and Executes Cleaning Validation Strategies: Creates plans, protocols (IQ, OQ, PQ), and risk assessments to ensure effective cleaning processes for medical devices and equipment.
- Ensures Regulatory Compliance: Adheres to FDA (21 CFR 820), ISO 13485, and other relevant regulations, participating in audits and maintaining up-to-date knowledge.
- Analyzes Data and Reports Findings: Compiles and analyzes validation data, writes comprehensive reports, and identifies trends for process improvement.
- Collaborates Cross-Functionally: Works with Manufacturing, Quality Assurance, Engineering, and other teams to implement cleaning strategies, resolve issues, and provide technical support.
- Manages and Improves Cleaning Processes: Leads continuous improvement initiatives, manages change controls, troubleshoots cleaning problems, and ensures proper documentation and training. Creating, maintaining, and improving controlled technical documents such as prints, procedures, bills of materials, and routers.
- Supporting a wide variety of processing applications such as machining, finishing, forging, casting, cleaning, heat treating, bonding, molding, etc.
- Conducting feasibility study to estimate a product cost and analyze capital equipment, capacity, and capability requirements.
- Establishing and improving process methods that meet performance and quality requirements.
- Developing and executing project plans and schedules for work activities.
- Communicate (written and verbal) direction and project plans with appropriate personnel from other departments.
- Evaluating multiple options to select the most appropriate processes and machining methods.
- Execute equipment qualification or process validation project(s).
Requirements:
- Experience supporting medical device manufacturing.
- Cleaning & Upgrade Validations.
- Specific experience with process characterization, equipment IQ/OQ, process OQ, and PQ.
- Specific experience with Test method Validation and Gage R&R.
- Experience with root cause analysis and problem-solving for both technical and process issues.
- Working knowledge of design control and cGMP requirements for medical device manufacturing per FDA QSR and ISO(phone number removed)Ability to lead and prioritize multiple medium-complexity project assignments and complete work in a timely manner.
- Good problem-solving skills using quality and statistical tools.
- BOM & Router creation and update.
- Ability to read and understand engineering drawings.
- Knowledge of basic quality tools, risk analysis (PFMEA), statistics (SPC), Critical-to Quality (CTQ) Analysis.
- Knowledge of Quality System requirements, ISO and FDA requirements.
- Ability to effectively work within a cross-functional team to complete critical project tasks.
- Demonstrates good written and verbal communication skills.
- Experienced with control procedures, such as the Change Management System, Nonconformance Reports, Engineering Specifications, Corrective and Preventive Action (CAPA), and Work Instructions & Proficient with Statistical Process Control concepts, process development, CNC programming terminology, and tooling design concepts.
- Microsoft Office Suite and Project.