Quantitative framework enables tunable elastomer curing via temperature control
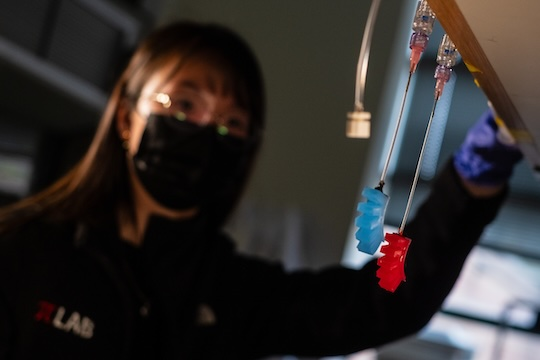
Te Faye Yap, a Rice University Ph.D. student in the Preston lab and lead author on a study published in Cell Reports Physical Science, demonstrates the performance of grippers cured at room temperature (blue) and at elevated temperatures (red) when pressurized. Credit: Jeff Fitlow/Rice University
Soft robots use pliant materials such as elastomers to interact safely with the human body and other challenging, delicate objects and environments. A team of Rice University researchers has developed an analytical model that can predict the curing time of platinum-catalyzed silicone elastomers as a function of temperature. The model could help reduce energy waste and improve throughput for elastomer-based components manufacturing.
“In our study, we looked at elastomers as a class of materials that enables soft robotics, a field that has seen a huge surge in growth over the past decade,” said Daniel Preston, a Rice assistant professor of mechanical engineering and corresponding author on a study published in Cell Reports Physical Science. “While there is some related research on materials like epoxies and even on several specific silicone elastomers, until now there was no detailed quantitative account of the curing reaction for many of the commercially available silicone elastomers that people are actually using to make soft robots. Our work fills that gap.”
The platinum-catalyzed silicone elastomers that Preston and his team studied typically start out as two viscoelastic liquids that, when mixed together, transform over time into a rubbery solid. As a liquid mixture, they can be poured into intricate molds and thus used for casting complex components. The curing process can occur at room temperature, but it can also be sped up using heat.
Manufacturing processes involving elastomers have typically relied on empirical estimates for temperature and duration to control the curing process. However, this ballpark approach makes it difficult to predict how elastomers will behave under varying curing conditions. Having a quantitative framework to determine exactly how temperature impacts curing speed will enable manufacturers to maximize efficiency and reduce waste.
“Previously, using existing models to predict elastomers’ curing behavior under varying temperature conditions was a much more challenging task,” said Te Faye Yap, a graduate student in the Preston lab who is lead author on the study. “There’s a huge need to make manufacturing processes more efficient and reduce waste, both in terms of energy consumption and materials.”
To understand how temperature impacts the curing process, the researchers used a rheometer ⎯ an instrument that measures the mechanical properties of liquids and soft solids ⎯ to analyze the curing behavior of six commercially available platinum-catalyzed elastomers.
“We were able to develop a model based on what is called the Arrhenius relationship that relates this curing reaction rate to the temperature at which the elastomer is being cured,” Preston said. “Now we have a really nice quantitative understanding of exactly how temperature impacts curing speed.”
The Arrhenius framework, a formula that relates the rate of chemical reactions to temperature, has been used in a variety of contexts such as semiconductor processing and virus inactivation. Preston and his group have used the framework in some of their prior work and found it also applies to curing reactions for materials like epoxies as described in previous studies. In this study, the researchers used the Arrhenius framework along with rheological data to develop an analytical model that could directly impact manufacturing practices.
“In this work, we really probed the curing reaction as a function of the temperature of the elastomer, but we also looked in depth at the mechanical properties of the elastomers when cured at elevated temperatures meant to achieve these higher throughputs and curing speeds,” Preston said.
The researchers conducted mechanical testing on elastomer samples that were cured at room temperature and at elevated temperatures to see whether heating treatments impact the materials’ mechanical properties.
“We found that exposing the elastomers to 70 degrees Celsius (158 Fahrenheit) does not alter the tensile and compressive properties of the material when compared to components that were cured at room temperature,” Yap said. “Moreover, to demonstrate the usage of accelerated curing when making a device, we fabricated soft, pneumatically actuated grippers at both elevated and room temperature conditions, and we observed no difference in the performance of the grippers upon pressurizing.”
While temperature did not seem to have an effect on the elastomers’ ability to withstand mechanical stress, the researchers found that it did impact adhesion between components.
“Say we’ve already cured a few different components that need to be assembled together into the complete, soft robotic system,” Preston said. “When we then try to adhere these components to each other, there’s an impact on the adhesion or the ability to stick them together. In this case, that is greatly affected by the extent of curing that has occurred before we tried to bond.”
The research advances scientific understanding of how temperature can be used to manipulate fabrication processes involving elastomers, which could open up the soft robotics design space for new or improved applications. One key area of interest is the biomedical industry.
“Surgical robots oftenbenefit from being compliant or soft in nature, because operating inside the human body means you want to minimize the risk of puncture or bruising to tissue or organs,” Preston said. “So a lot of the robots that now operate inside the human body are moving to softer architectures and are benefiting from that. Some researchers have also started to look into using soft robotic systems to help reposition patients confined to a bed for long periods of time to try to avoid putting pressure on certain areas.”
Other areas of potential use for soft robotics are agriculture (for instance picking fruits or vegetables that are fragile or bruise easily), disaster relief (search-and-rescue operations in impacted areas with limited or difficult access) and research (collecting or handling samples).
“This study provides a framework that could expand the design space for manufacturing with thermally cured elastomers to create complex structures that exhibit high elasticity which can be used to develop medical devices, shock absorbers and soft robots,” Yap said.
Silicone elastomers’ unique properties ⎯ biocompatibility, flexibility, thermal resistance, shock absorption, insulation and more ⎯ will continue to be an asset in a range of industries, and the current research can help expand and improve their use beyond current capabilities.
Source: Rice University
Published on March 19, 2024